Custom Metal Injection Molding Parts and Components for Industry
RCT MFG offers our customers new dimensions of shape complexity and component performance by utilizing Metal Injection Molding (MIM). MIM can economically produce complex shapes that are beyond the capabilities of traditional powder metallurgy.
Metal Injection Molding is able to manufacture parts with features such as OD/ID threads and undercuts without the need for secondary operations. In addition, the fine grain size used in Metal Injection Molding feedstocks allows for sintered densities close to theoretical density, while 80~90% of the density is achieved through traditional pressing/sintering. The combination of fine grain size and high density gives MIM components properties that match their forged counterparts.
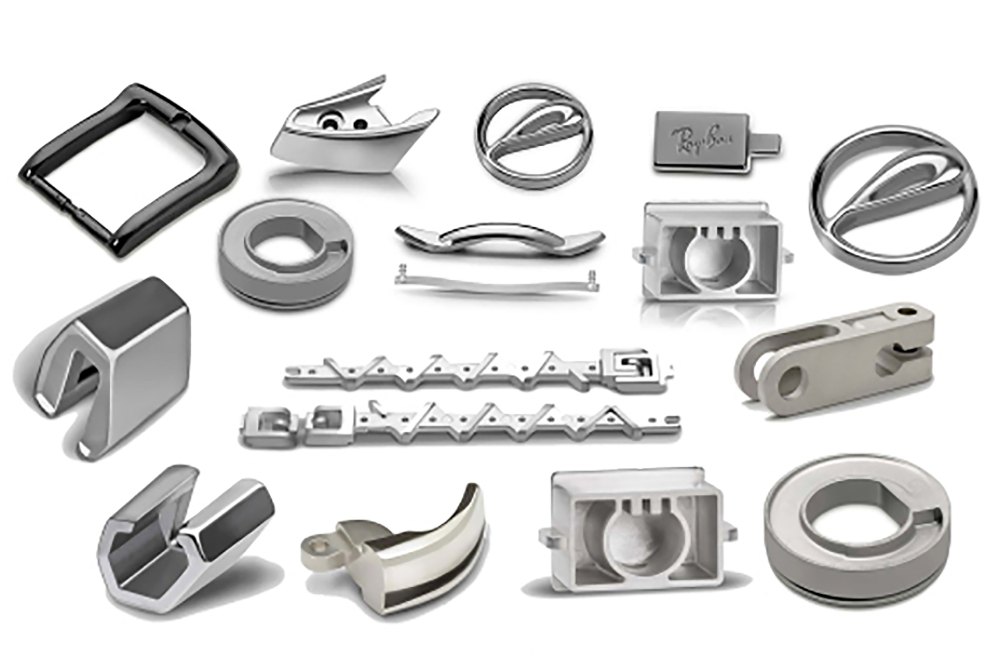
What is Metal Injection Molding?
So what is MIM? Metal injection molding (MIM) is a core metalworking process that allows manufacturers to create custom metal parts in complex shapes. MIM enables one to create any kind of metal body. It is primarily employed in the making of small, complex, tailored metal parts that are not readily available in the market and must be custom made. These parts generally weigh less than 100 grams.
The MIM process allows for considerably more design freedom than other metal fabrication processes like die casting. You can choose from almost any combination of metal powder and plastic binders to produce even the most complex shapes.
Metal Injection Moulding (MIM) capability overview
Metal Injection Moulding (MIM) | |
---|---|
Maximum part size |
Product weight up to 500g
Depending on the geometry, 1000g may be possible
Typical max dimension 25 - 35mm, ranging up to 200mm
|
Tool lead time | 25 - 40 days |
Typical tool life | 200,000 - 300,000 cycles |
FOTS (First off-tool) lead time | 5 - 10 days |
Wall thickness | 2 - 3mm (typical), down to 0.1mm min |
Standard linear tolerance |
< 5mm, ± 0.025 mm
5 - 10mm, ± 0.05 mm
10 - 20mm, ± 0.07 mm
20 - 30mm, ± 0.15 mm
30 - 60mm, ± 0.25 mm
> 60mm, ± 0.5%
|
Surface roughness | Ra 0.8 - 1.5 |
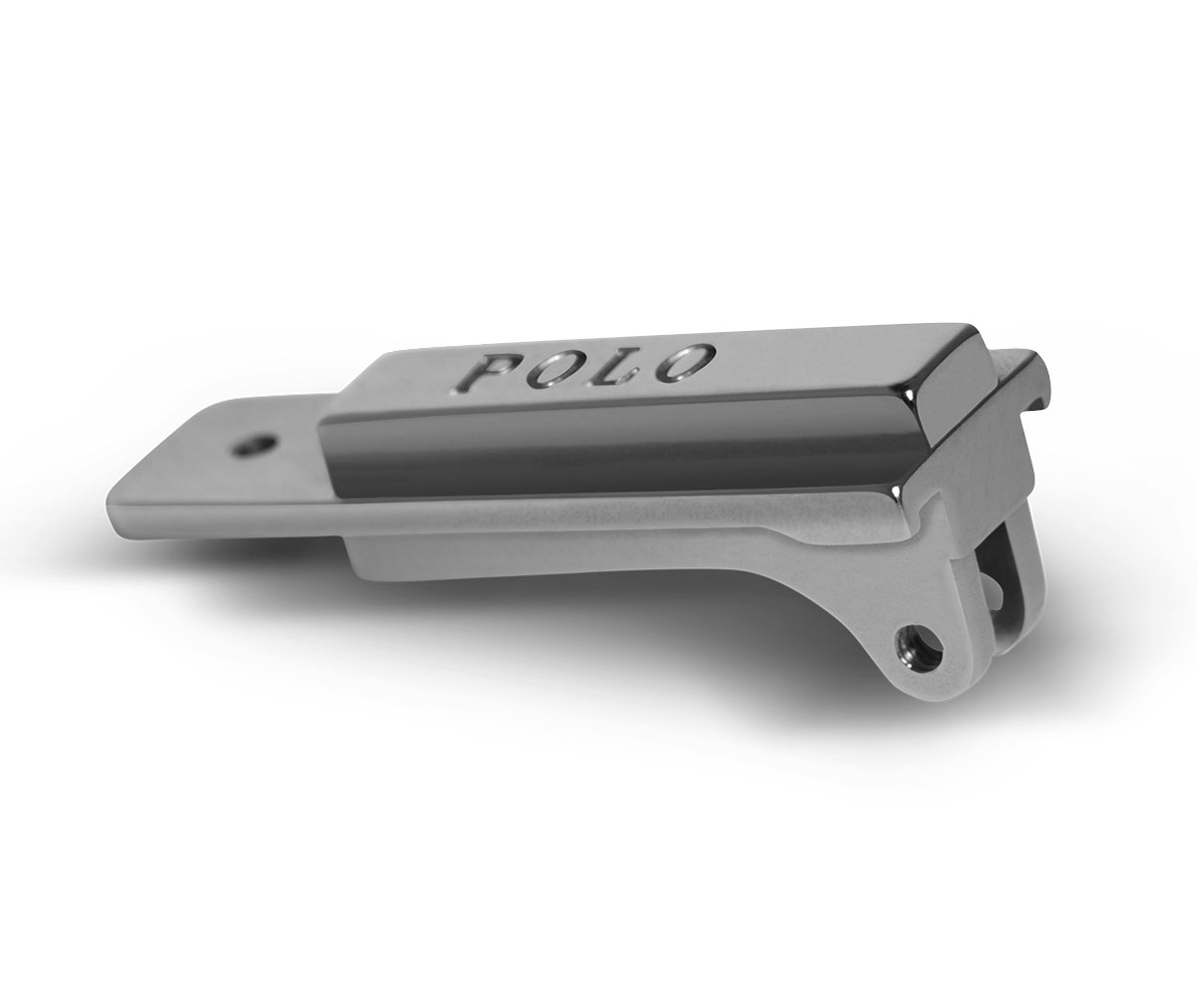
Metal Injection Molding Advantages and Disadvantages
Metal molding has some distinct advantages compared to other manufacturing processes. Some of them include:
1. Complex Shapes: Can produce metal injection molded parts with intricate details, thin walls, sharp internal corners, undercuts, and more, all within a single operation.
2. Reduction of Assemblies: Combining what would typically require multiple parts made from other processes into a single component is possible with the MIM process. Consolidating the design simplifies your assemblies and reduces cost.
3. Accuracy: Critical tolerances can be achieved with highly repeatable results. Parts can be post-machined for extra tight dimensions and features.
4. High-Performance Materials: Get tough, high-performance parts made using materials such as stainless steel. MIM is best suited for high melting temperature materials versus softer materials such as aluminum or zinc that are a better fit for die casting.
5. Cost and Speed: Ideal for optimizing production run cost with return on investment for high volumes and rapid production of small, complex parts.
6. Broad Industry Support: Due to the ability to mass-produce parts from biocompatible and hardened materials, MIM is used in medical, firearms, aerospace, and other industries.
Have an upcoming metal injection molding project?
Metal Injection Molding VS CNC Machining
Metal Injection Molding Services
1. Uses custom mold (requires additional lead time and cost)
2. Expensive to redesign (requires the creation of new mold)
3. Fastest part production
4. Cheaper cost per part with high quantity runs
5. Ideal for producing parts made from softer plastics
6. Rubber and flexible materials can use this method
CNC Machining Services
1. Uses CAD file for production
2. Allows for cheaper design iteration
3. Rapid part production (not as fast as injection molding)
4. Cheaper for smaller quantity runs
5. Best for harder plastics
6. Larger variety of materials available
7. Allows for tighter tolerance and surface finishing
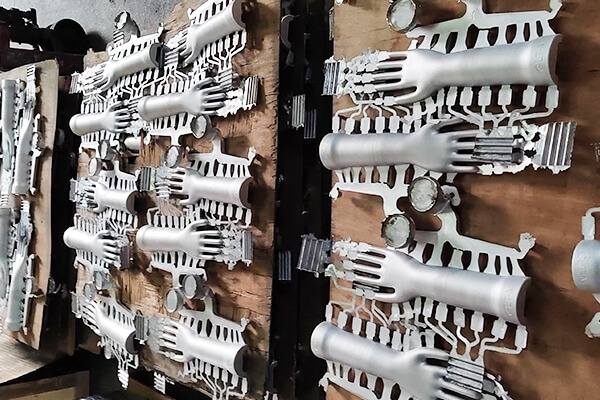
Metal Injection Molding Materials
1. Stainless Steel: 304L, 316L, 17-4 PH, 15-5 PH, 420, 430, 440
2. Superalloys: Inconel, Hastelloy, Co-based Low Alloy Steels, 2-8% Ni (4600, 4650)
3. Magnetic Alloys: 2-6% Si-Fe, 50% Ni-Fe, 50% Co-Fe
4. Controlled Expansion Alloys: Fe-36Ni (Invar), F-15 (Kovar)
5. Electrical Materials: Pure Copper, Beryllium-Copper, Brass
6. Tool Steels: AISI M2, M3/2, M4, T15, M42, D2
7. Heavy Alloys: Tungsten-Copper, W-Fe-Ni, Molybdenum-Copper, Custom compostions to suit customer specifications
Markets Served
1. Automotive
2. Aerospace
3. Medical
4. Business Machine
5. Computer Components
6. Hardware
7. Sporting and Consumer Goods
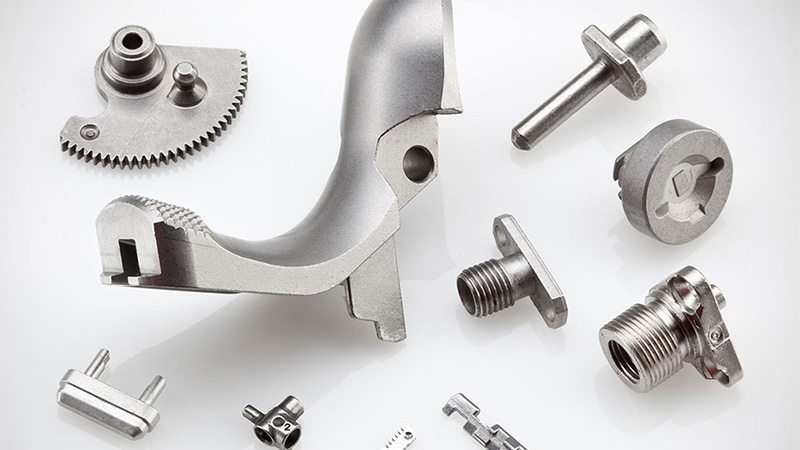
Have a Metal Injection part? Bring it on!
We enjoy the challenge of complex parts others have failed to create. We are a leader in producing high quality, tight tolerance component parts from round stock, shaped stock, cast and forged materials serving a wide range of industries for our customers around the globe.