Low Volume Production Automative spare parts Urethane Casting
What Is Urethane Casting?
Urethane casting uses a softer silicone mold in comparison to the harder machined molds used in injection molding. The process produces urethane materials that may be rigid or flexible. Urethane molding is a fast fabrication process that can create complex parts, components, and tools with the use of detailed silicone molds. These silicone molds may be simple or incorporate complex design geometries.
1. Product Parameter for Low Volume Production Automative spare parts Urethane Casting
Vacuum casting is a low-cost but reliable method for making a small number of high-quality prototypes based on a master model. This method is ideal for rapid prototyping used in engineering testing, proof-of-concept and display demos. On superior prototype, we have a dedicated team of mold makers who are experts at creating vacuum casting molds for many years.
● Low initial cost since it no need to invest in tooling
● The high fidelity of the mold gives excellent surface details requiring little or no post-processing
● Many different molding polymers are available that can be pigmented to meet your color requirements
● Molds can be ready in a few days once the master model has been created
● Molds are durable up to approximately 50 copies so it’s great if you need more than one copy
● We provide overmolding, so that different types and hardness of plastic can be molded together into a single unit
● It is an excellent option for testing multiple variations of a prototype design for rapid product development
Urethane Casting Materials
Careful material selection is an important part of the design process. A variety of polyurethane materials can be used in urethane casting. Material selection depends largely on the desired physical properties of the end part. In addition, additives can be added to most materials that result in different colors, finishes, and textures.
1. Elastomeric (Shore A). Shore A urethane-based materials are soft and flexible.
2. Rigid (Shore D). This classification of material is rigid. It creates impact-resistant and rugged products.
3. Expanding Foam. Foams can range from soft and low-density to high-density and rigid.
4. Silicone Rubber. These composite materials are usually platinum-based and are used to form small high-contact parts.
Various materials and additive mixtures can be used to meet a variety of industry standards, such as UL 94-VO and FAR 25.853 ratings regarding flammability, flame exposure, and exposure to high temperatures or the cleanliness standards found in many pharmaceutical and medical applications
Urethane molding is a popular fabrication process across multiple industries because it produces durable, affordable parts quickly.
The following industries commonly use urethane casting:
● Aerospace
● Automation
● Automotive
● Consumer products
● Dental and medical
● Electronics
● Industrial production
●Military and defense
●Robotics
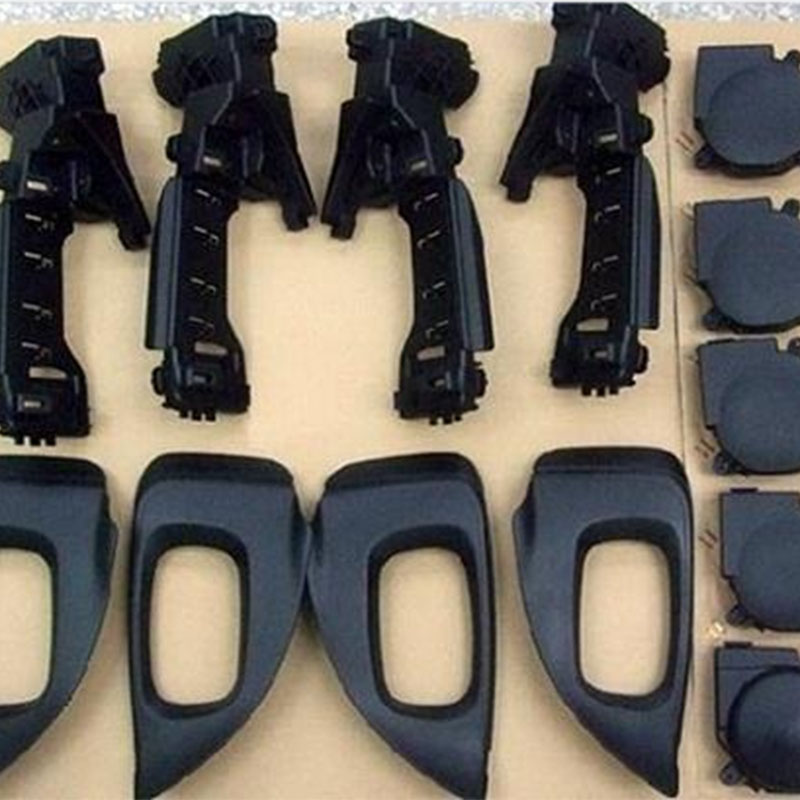
Applications of Urethane Casting / Design Analysis / Alpha/Beta builds / Color/Texture studies / Packaging test / Show models / Large volume prototypes / Low volume production / Low volume production
Product Details for Low Volume Production Automative spare parts Urethane Casting
The success of some products depends on how quick you can enter the market. When time is of the essence, RCT CNC machining and vacuum casting and rapid machining technology can provide you with low-volume manufacturing quickly. These technologies can serve almost all engineering materials, including thermoplastics, aluminum and metals, and advanced polyurethanes. It can serve as a bridge between tools and molds, on the same time it can be applied to market research for new design.
Mold machining Machines
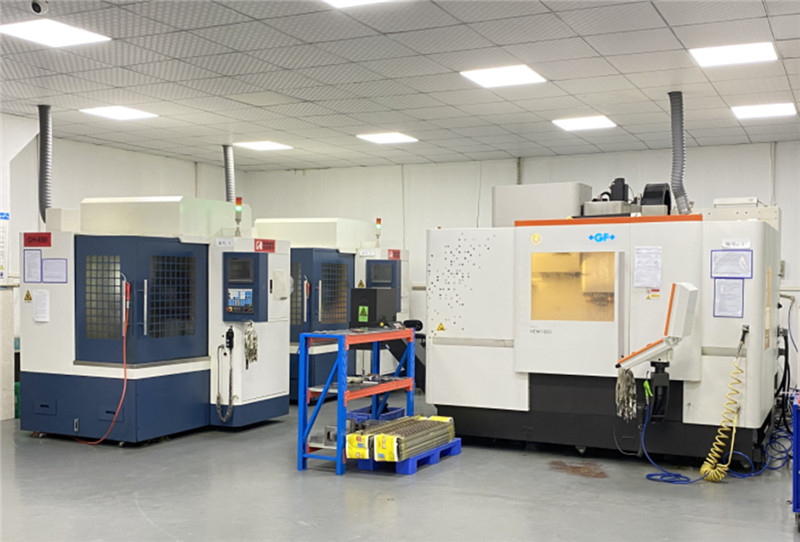
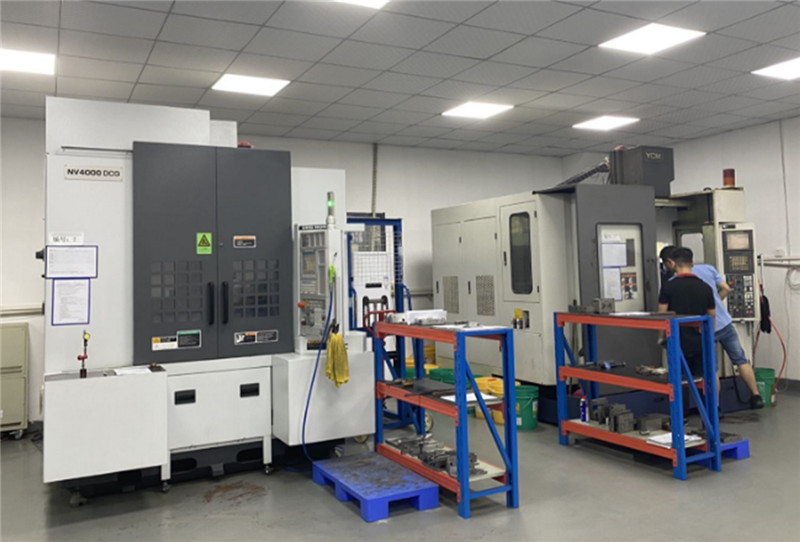
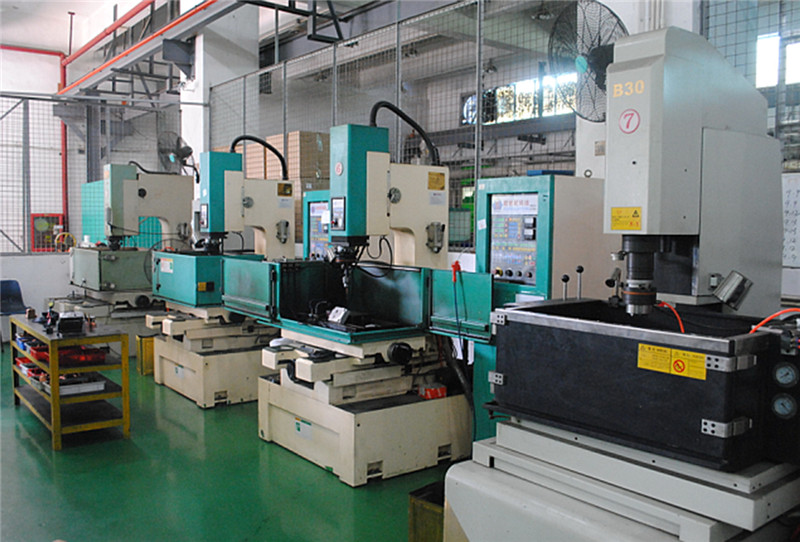
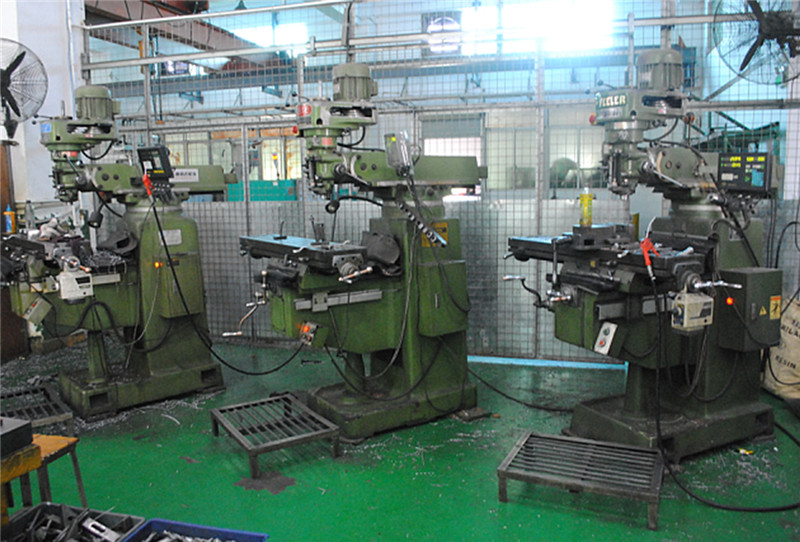
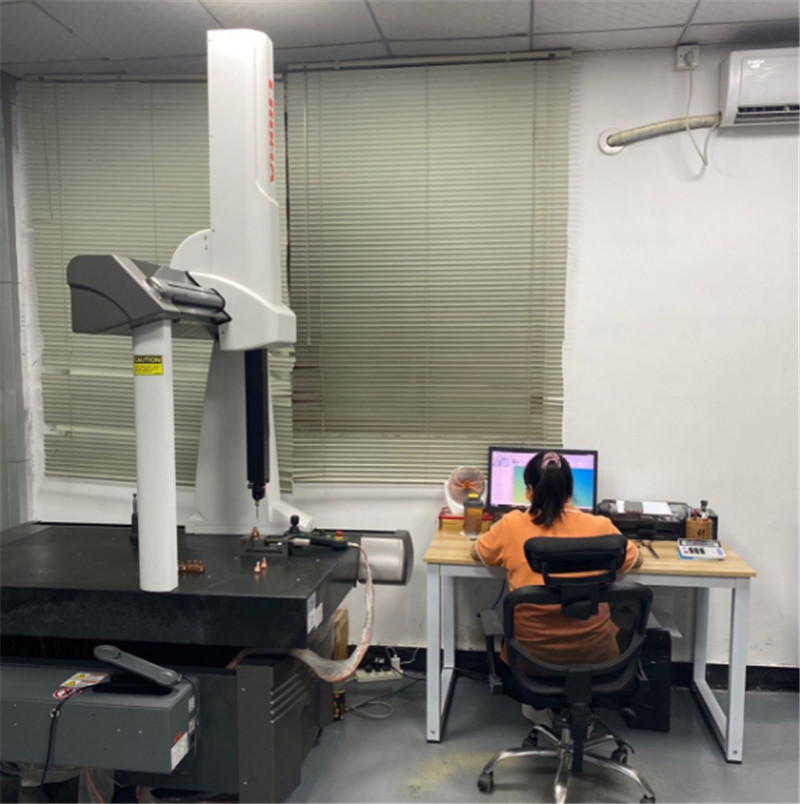