Custom Molded Rubber and Silicone Parts
RCT MFG specializes in liquid silicone rubber (LSR) molding and compression molding of rubber parts. These two processes create highly detailed and precise molds that facilitate the creation of commercial and industrial rubber parts. These services offer an ideal solution for rapid prototyping, small production runs, and production runs for companies trialing new products.
Liquid silicone rubber (LSR) molding is a thermoset process that mixes a two-component compound together, which is then heat cured in the mold with a platinum catalyst to produce a final part. LSR parts are created through an injection molding process where the material delivery system is cooled and the mold is heated.
RCT MFG also specializes in the compression molding of rubber parts. Typical applications for this method are electric connectors, medical devices, seals, kitchen cookware, and miscellaneous products.
RCT MFG Capabilities
Service | Details |
---|---|
Lead Time |
Starts at 15 business days, including 24-hour quote responses with design-for-manufacturing (DFM) feedback |
Production Options |
Domestic and international |
Machines Available |
Single, multi-cavity, and family molds; 50 to 1,100+ press tonnage; side actions including hand-loaded cores |
Inspection and Certification Options |
Includes FAI and PPAP. ISO 9001, AS9100, ISO 13485, UL, ITAR, and ISO 7 and 8 Medical Clean Room molding. |
Tool Ownership |
Customer-owned with mold maintenance |
Mold Cavity Tolerances |
+/- 0.005" when machining the mold and an additional +/- 0.002" per inch when calculating for shrink rate |
Part to Part Repeatability |
+/- 0.004" or less |
Critical Feature Tolerances |
Tighter tolerances can be requested and may increase the cost of tooling because of additional sampling and grooming. RCT MFG will mill to a steel-safe condition on critical features. |
Available Mold Types |
Steel and aluminum; Production grades range from Class 105, a prototype mold, to Class 101, an extremely high production mold. RCT MFG typically produces Class 104, 103, and 102 tools. |
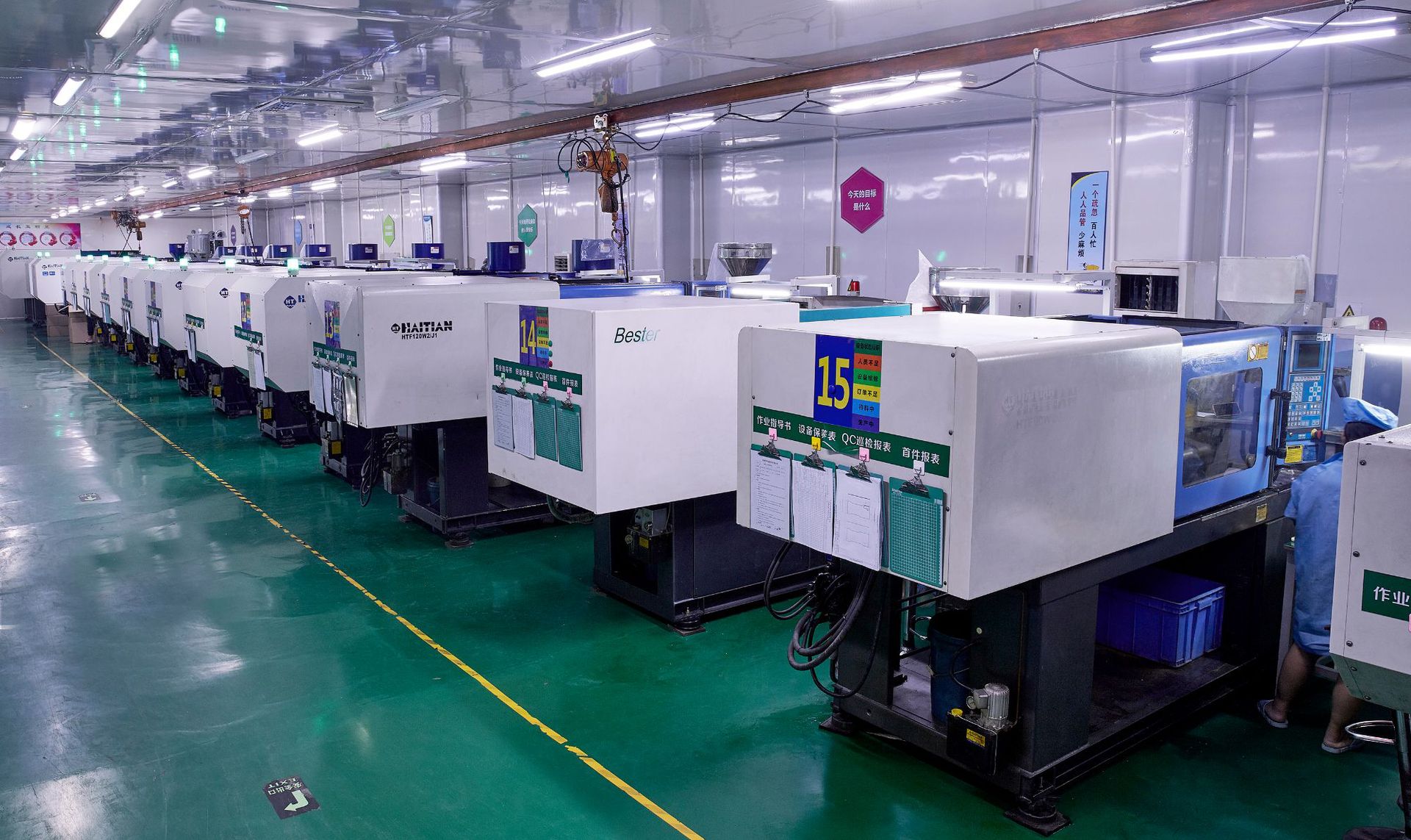
Transitioning from Flat Prototypes to Molded Production Parts
On occasion, customers want to transition from flat cut parts to molded components. As customers work through small prototype runs of initial designs, RCT MFG supports this change with quick turn waterjet cut gaskets using molded LSR sheets. As designs develop and molding is required, the same material can be utilized. This eliminates re-testing and re-validation, since the material is the exact same for the prototypes and production parts.
For parts without any sort of 3D geometry, molding can be a very cost effective solution at high quantity production, as traditional die-cutting and waterjet cutting have wasted material cost. For example, a small window gasket may be quite cost effective to provide in small quantities as a waterjet cut part, but as production quantities increase, the combined cost of the wasted window cutout can add up. In cases like this, paying to tool-up a production LSR mold creates a much more cost-effective solution trimmed piece price down the line.
Ready to Get an LSR Injection Molding Quote?
Liquid Silicone Rubber Materials
- Standard Silicone (30, 40, 50, 60, and 70 durometers)
- Medical-Grade Silicone
- Optical-Grade Silicone
- Fluorosilicone (fuel and oil resistant)
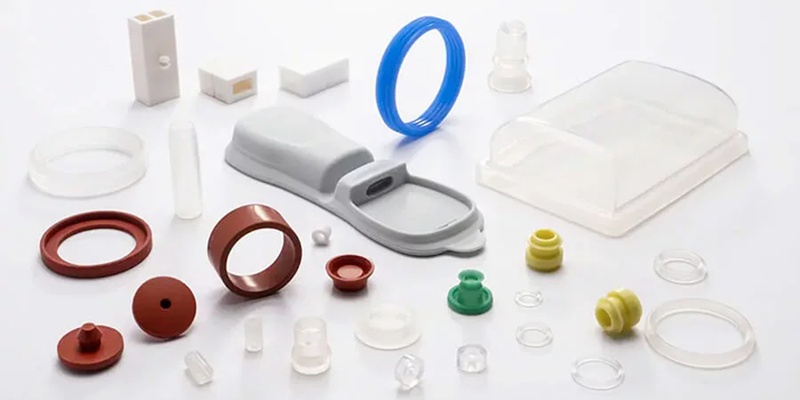
Surface Finish Options
FINISH | DESCRIPTION |
---|---|
PM-F0 | non-cosmetic, finish to Protolabs' discretion |
PM-F1 | low-cosmetic, most toolmarks removed |
PM-F2 | non-cosmetic, EDM permissible |
SPI-C1 | 600 grit stone, 10-12 Ra |
PM-T1 | SPI-C1 + light bead blast |
PM-T2 | SPI-C1 + medium bead blast |
SPI-B1 | 600 grit paper, 2-3 Ra |
SPI-A2 | grade #2 diamond buff, 1-2 Ra |
What is LSR Molding?
Liquid silicone rubber, or LSR, injection molding is a thermoset process that mixes two compounds together. This two-component compound is heat cured in a mold along with a catalyst which results in a completed molded part. Liquid Silicone Rubber – LSR – components are produced via an injection molding process comparable to plastic injection molding. However, there is a major difference between the two processes in that the material delivery system is cooled and the mold is heated. Liquid silicone rubber injection molding is different from the plastic injection molding process because it centers on mechanical mixing as opposed to pressurized impingement mixing.
Liquid silicone rubbers are cross linked via a platinum-catalyzed reaction. After curing, LSR’s cannot be reshaped or repurposed because it would take a high level of energy to break apart the cross-linked material. The structural make-up of LSR makes it useful for a wide range of temperatures and the bonds between the silicon and oxygen atoms means the polymer will not degrade easily. One liquid silicone rubber’s major advantage is the chemical inertness or purity. Combined with its ability to withstand sterilization processes, this makes LSR’s ideal for many medical uses. Most of liquid injection moldings, or LIM molding, is the result of the versatile properties of liquid silicone. Liquid silicone rubber possesses a high degree of heat resistance, high tensile strength, and flexibility. LSR also is very formable and may be colored or transparent as a finished product. Liquid silicone may also serve as excellent insulators or conductors depending on the exact compound composition.
Advantages of liquid silicone injection molding
Liquid silicone injection molding combines two sets of benefits: the high-quality, high-volume production capabilities of injection molding, and the elastomeric material properties of liquid silicone rubber. Key advantages include:
1. Efficiency: The mold injection process is highly efficient, enabling the fast production of large orders.
2. Detail: The high pressure of injection ensures that liquid silicone reaches every crevice of the mold before curing—even more effectively than a melted thermoplastic.
3. Increased design freedom: Silicone parts do not need to be uniformly cooled and are easy to remove from a metal mold, enabling greater design freedom.
4. Material properties: Silicone parts have excellent thermal, chemical, and electrical resistance, as well as a low compression set.
5. Affordability: Fast and efficient production ensures a low cost per part. Liquid silicone rubber works particularly well with low-cost aluminum molds, further reducing costs.
6. High-volume production: Injection molding can facilitate high-volume production of silicone parts into the millions.
Limitations of liquid silicone injection molding include the non-reformability and non-recyclability of thermoset parts, the high up-front cost of tooling (which can result in a high cost per part when dealing with low volumes), certain design restrictions, and the extra time needed to mix the two liquid components.
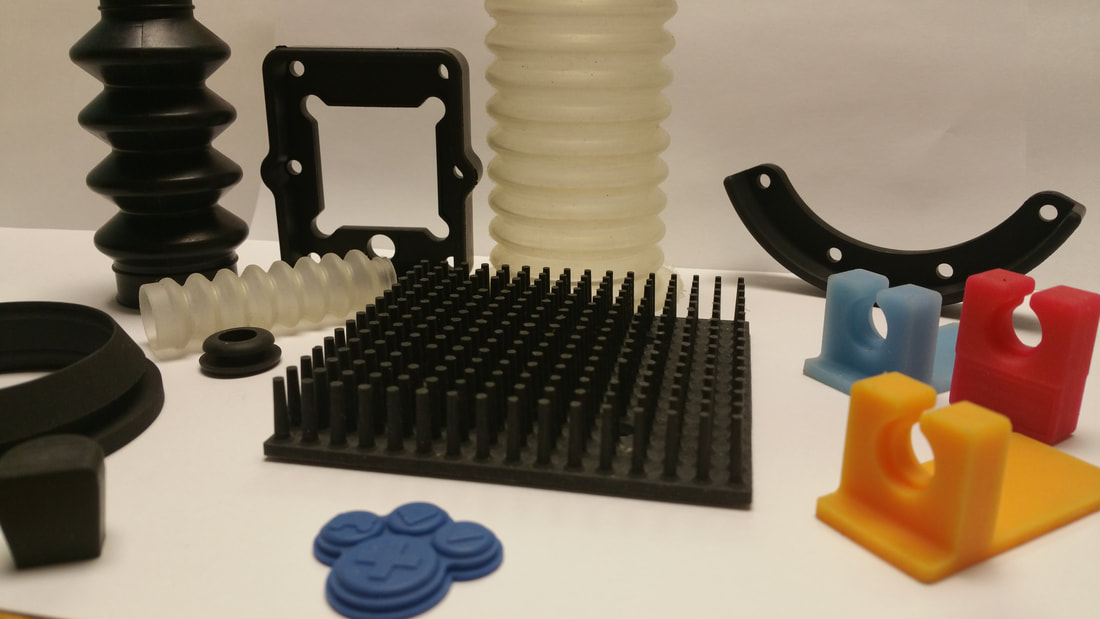
Alternatives
There are ways to create silicone-like parts without liquid silicone injection molding, by using an alternative process and/or material.
From a process perspective, the closest alternative is the injection molding of thermoplastic elastomers (TPE) or thermoplastic vulcanizates (TPV): these are pliable, impact-resistant plastics that are melted, injected, and solidified like other thermoplastics. An advantage of these materials is that they do not require metering and mixing. But although they have elastomeric properties, TPE and TPV are subject to theromoplastic weaknesses such as degradation in sunlight, and may not be suitable for certain medical applications.
Beyond injection molding, TPE is one of a handful of materials that can be made into a flexible 3D printing filament: a material used to additively manufacture rubberlike parts. TPU is another such material.
Request a Free Quote Today
For a free quote within 24 hours call RCT MFG today. Our team is ready to answer any questions you may have, will deliver LSR quotes within 24 hours, and will provide a free DFM within 48 hours.