Precision Turned Part Manufacturing
We use state-of-the-art CNC lathes to produce turned metal parts to tight tolerances for all applications in a wide range of industries. Using metal bar stock up to 1.25” OD, we can machine surfaces and planes to tolerances up to ±0.0005”, and feature locations and profiles to ±0.0005”.
Even the most complex or sophisticated part designs can be accurately reproduced with perfect repeatability from the first to the 100,000th piece. We work from your CAD or other digital design files to provide precision turned parts to your exact specifications, with DFM services available.
RCT MFG specializes in high-volume CNC turning. We can turn and machine tens to hundreds of thousands of parts or more. This allows us to run our CNC lathes for extended periods of time with a single tool setup, resulting in faster, more efficient production. We have uninterrupted manufacturing capabilities, including “lights out” production using automated CNC technology, enabling 24/6 production.
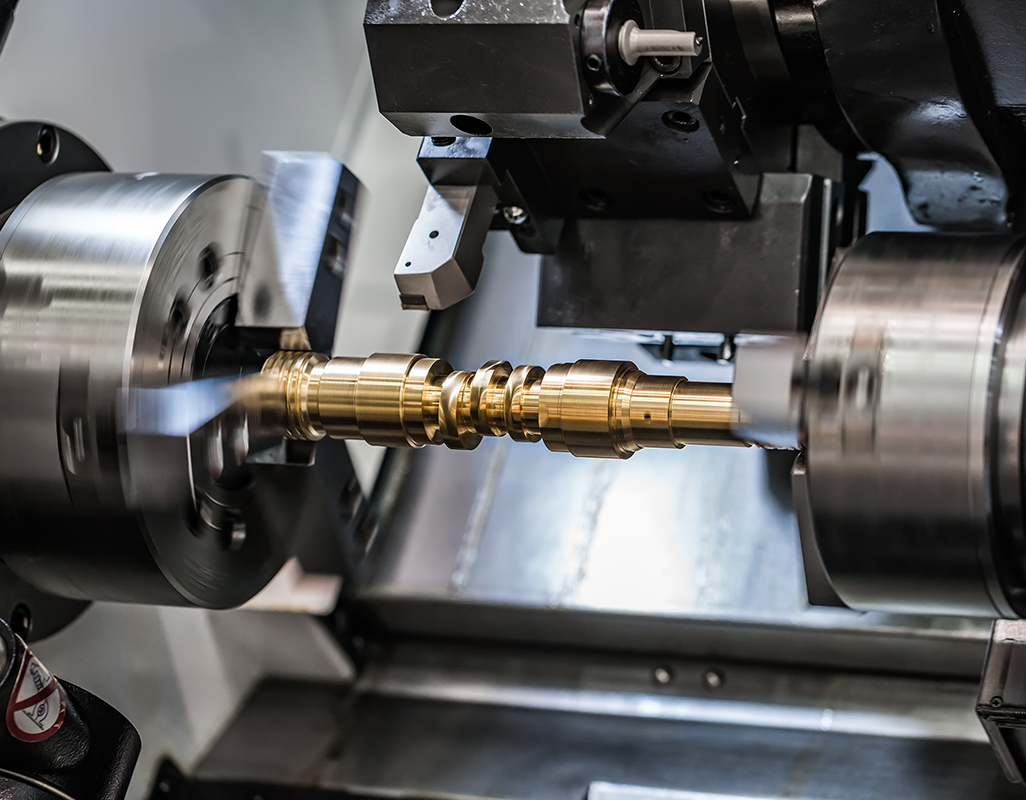
CNC Turning vs CNC Milling
CNC milling and turning allow users to create patterns and add detail to metals that are impossible to do by hand. However, CNC Milling and CNC Turning are very different processes that usually end up with entirely different results. They both use computer programming to achieve their end results, but the differences lie in the way their finalized parts are created.
For example, CNC milling drills and turns its material along an axis to cut its materials to their specified dimensions. Conversely, CNC turning uses a single-point cutting tool that maintains a parallel insert to cut its intended material. Furthermore, the material is rotated at changing speeds at which the cutting tool traverses to make its specified cylindrical cuts. The form, shape and dimensions of the finalized product will dictate whether CNC milling or CNC turning is appropriate for your given project.
CNC General Tolearances
Description | General Tolerance |
---|---|
Distance Dimensions |
For features of size (Length, width, height, diameter) and location (position, concentricity, symmetry) +/- 0.005”. |
Orientation and Form Dimensions |
0-12" +/- 0.005", Angularity 1/2 degree. For 24" and beyond please consult Xometry's Manufacturing Standards. |
Edge Condition |
Sharp edges will be broken and deburred by default. Critical edges that must be left sharp should be noted and specified on a print. |
Types of CNC Turning Processes
There are several types of turning processes, each of which perform different tasks to reach an expected outcome. While none of these processes achieve much separately, mixing and matching them all and incorporating computer programming results in high quality parts. Some primary types of turning include:
1. Straight or cylindrical turning. This type of turning uses a uniform motion to decrease the work diameter to prevent variation of the cut. This process removes large amounts of material from the workpiece before it undergoes more precise cuts.
2. Grooving. This process creates a narrow cavity by pressing a shaped tool into the material.
3. Taper turning. Taper turning creates a cylindrical shape with a gradually decreasing diameter.
4. Knurling. Often performed on materials that need extra grip, this process cuts a serrated pattern into the workpiece.
5. Spherical generation. This process results in a perfect sphere shape by turning the workpiece around a fixed axis of revolution.
6. Parting. This process removes a completed piece from the original stock piece by gouging deeply into the material.
7. Threading. Threading results in helical grooves that can be screwed into other components.
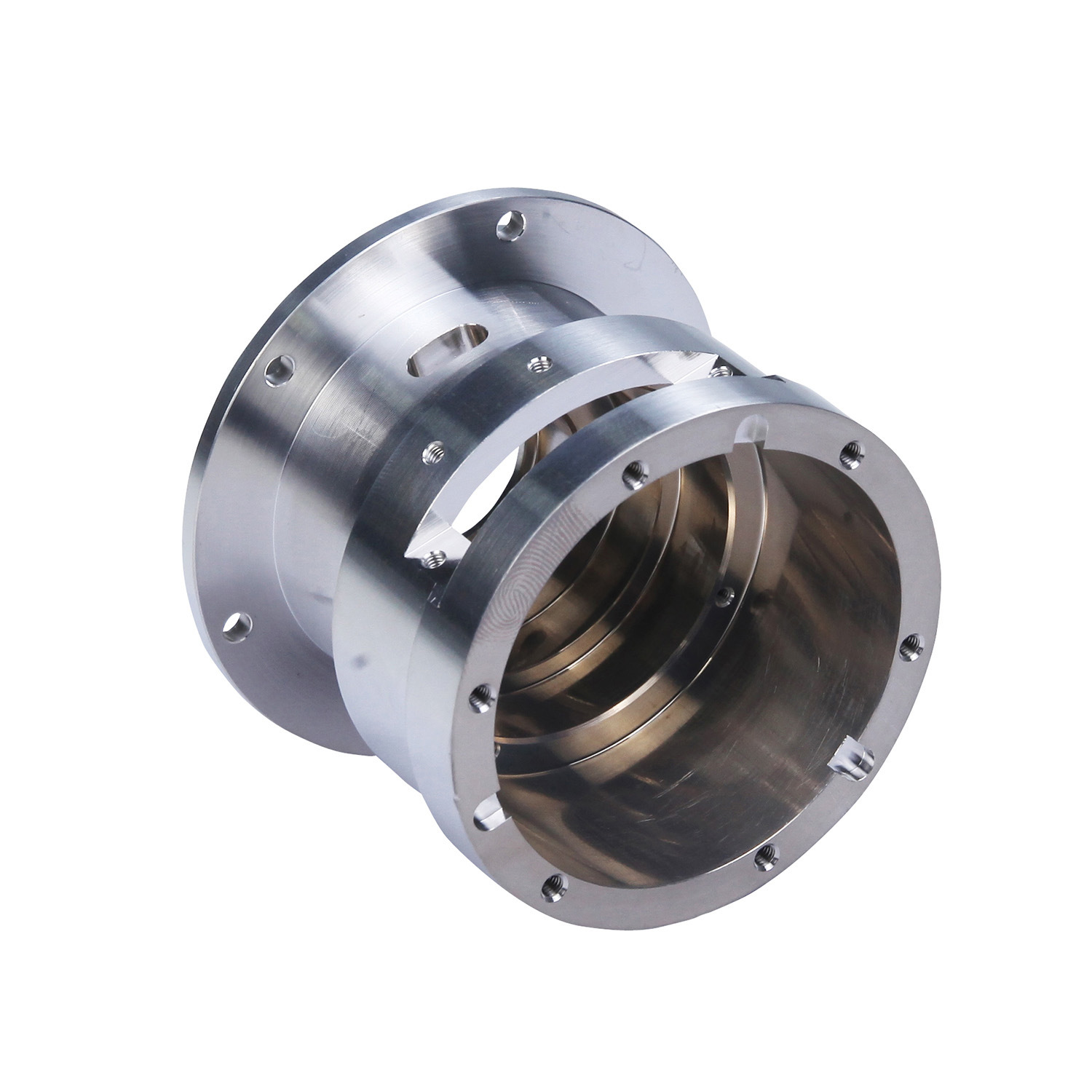
Ready to get started on your CNC turning quote?
What Is CNC Turning?
In the CNC turning process, otherwise known as subtractive machining, a chuck holds a bar of material, such as plastic or metal, in place. The piece rotates on a lathe, allowing a computer-controlled turret with attached tooling to cut the material into a specified shape based on programmed instructions. The more tools a turret can hold, the more complex options are available for the part. CNC lathes and turning centers can utilize a variety of processes to create different end results.
Advantages of CNC Turning with RCT MFG
Some direct benefits related to bar fed precision turned parts include:
1. Improves machining accuracy
2. Enables complex detail
3. Creates flexibility in manufacturing
4. Increases safety
5. Boosts production volume
6. Reduces setup-changeover time
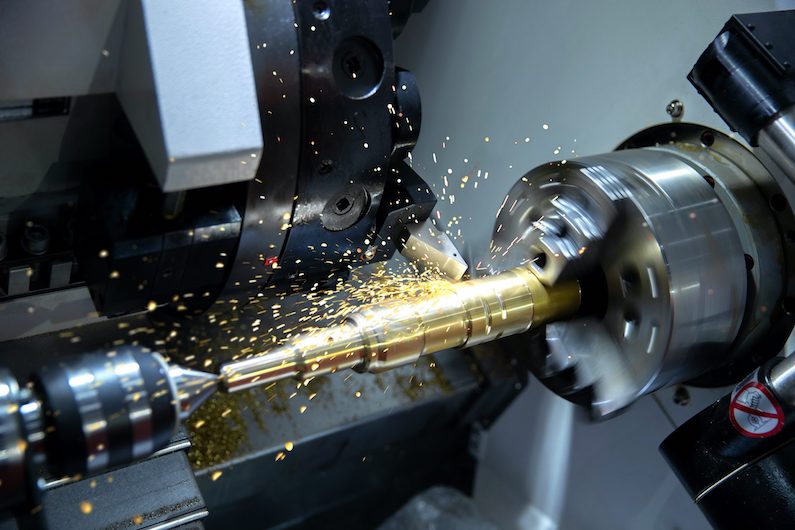
Material
All standard metals, aluminum, armor plate, brass, bronze, chromium, copper, gammalloy, Hastelloy, Incoloy, Inconel, Invar, manganese, Monel, nickel, Nitralloy, powdered metals, stainless steel, steel ,Stellite, titanium, Waspaloy, and many other superalloys
Secondary surface finishing processes
CNC lathe production can involve a variety of secondary finishes to ensure that the metal parts meet the desired surface quality after they have finished the machining process A secondary finishing service can include deburring, grinding, polishing, anodizing, painting, and plating. Deburring helps to remove any sharp edges or burrs, while grinding and polishing can improve the surface finish of the metal. Anodizing and plating can improve the strength, wear resistance, and corrosion resistance of the metal, and painting or powder coating, if the machined part is metal, can be used to add color to the part.
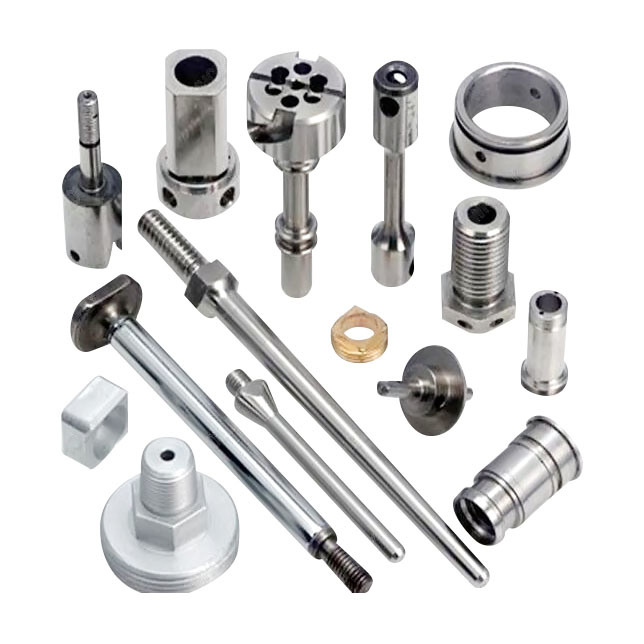
Industries We Serve
The clients from the following industries regularly utilize our CNC turning services.
Automotive
Medical Devices
Computer
Instrumentation
Hydraulics and Pneumatics
Flow Control
Security Systems
Aerospace and Defense
Agriculture
Heating, Ventilation and Air-conditioning (HVAC)
Mechanical and Heavy Equipment
Marine
Water Treatment
Choosing a CNC turning manufacturer for your next project
When choosing a CNC turning manufacturer for your project, it is important to consider the quality of the parts they produce, the secondary surface finishes they can accommodate, their turnaround time, and their customer service support. It is important to make sure that the manufacturer is up to date on the latest technology and has the necessary CNC machines to produce the parts you need in a cost-effective and reliable production run. Additionally, it is important to make sure that the manufacturer is experienced in the types of machining the CAD design may require such as tooling components, raw material acquisition, and access to a CNC milling machine to accommodate any advanced features. Finally, you should make sure that the cost of the parts is within your budget and is competitive with other quotes you have received.
Contact Us for CNC Turning Experts
RCT MFG is the right choice for all your fabrication needs. As a full-service shop, we offer everything from CNC machining to CNC metal fabrication, welding, painting, and assembly. You can trust us to get the job done on time. Contact us to discuss your requirements with one of our CNC turning experts.