Quality CNC Milling Service
If you are looking for a reliable, high-quality CNC milling service shop with a relatively low cost of machining parts, Ruitai Milling Service is a good choice. We have automated and advanced CNC lathes to meet complex parts processing. Whether you need 3-axis or 5-axis machining, Ruitai can provide feedback on your custom CNC milled parts.
Our milled parts process can be used for prototyping and low-volume manufacturing, CNC milling projects are used in various industries around the world and can be used for the manufacture of machined parts in a variety of metals, plastic polymers, wood, and other prototype materials.
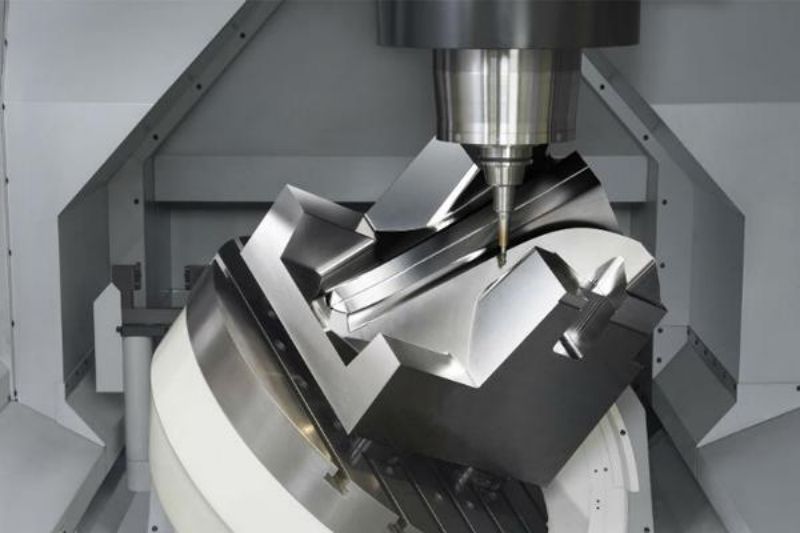
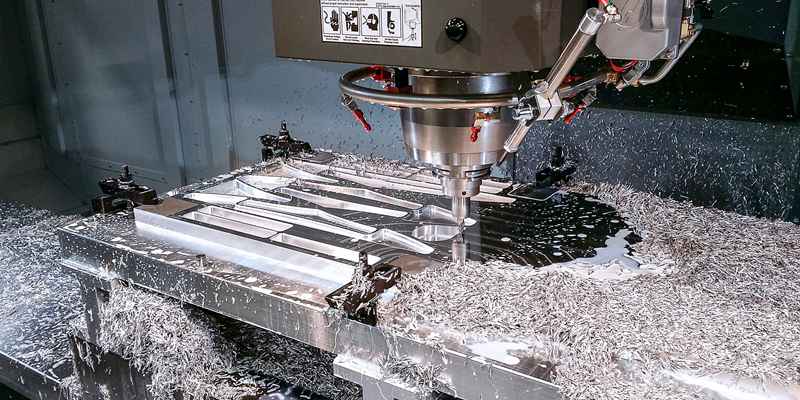
Metal CNC Milling Service
Metal CNC milling is a CNC Machining technology that can cut common metals in daily life, making them parts with high precision and strict tolerances. In Ruitai, we provide dozens of metal raw materials for you to choose. After milling The final machined Metal parts have precise shapes. Our Metal CNC milling processing services have high production efficiency. If you need to process metal accessories, then CNC milling is a good solution.
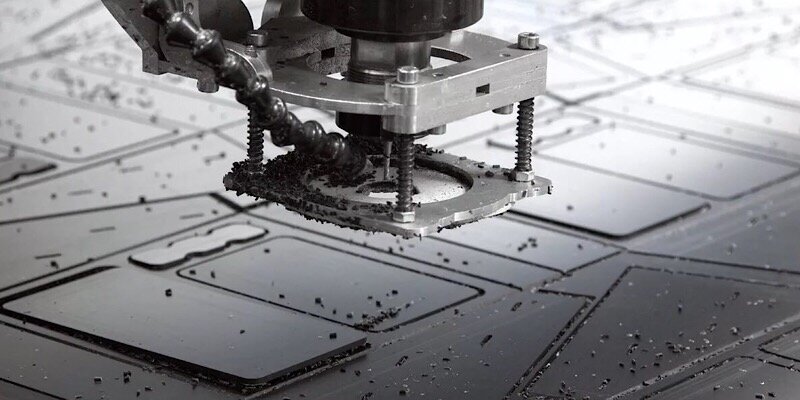
Plastic CNC Milling Service
If low-cost machining is your consideration for part machining, plastic CNC milling services are a win-win. Plastic CNC milling is machined with cost-effective polymer plastics, which can optimize your budget. Usually, its processing time is much shorter than that of wood and metal. Our platform provides many types of polymers. Plastic raw materials are your choice.
CNC Milling Tolerances & Standards
Description | General Tolerance or Standard |
---|---|
Maximum Part Size |
Milled parts up to 80” x 48” x 24” (2,032 x 1,219 x 610 mm). |
Distance Dimensions |
For features of size (Length, width, height, diameter) and location (position, concentricity, symmetry) +/- 0.005”. |
Orientation and Form Dimensions |
0-12" +/- 0.005", Angularity 1/2 degree. For 24" and beyond please consult Xometry's Manufacturing Standards. |
Precision Tolerances |
Xometry can manufacture and inspect to tight tolerances, including sub +/- 0.001" tolerances, per your drawing specifications and GD&T callouts. |
Minimum Feature Size |
0.020” (0.50 mm). This may vary depending on part geometry and chosen material. |
Threads and Tapped Holes |
Xometry can accommodate any standard thread size. We can also machine custom threads; these will require a manual quote review. |
Surface Finish |
The standard finish is as-machined: 125 Ra or better. Additional finishing options can be specified when getting a quote. |
Edge Condition |
Sharp edges will be broken and deburred by default. Critical edges that must be left sharp should be noted and specified on a print. |
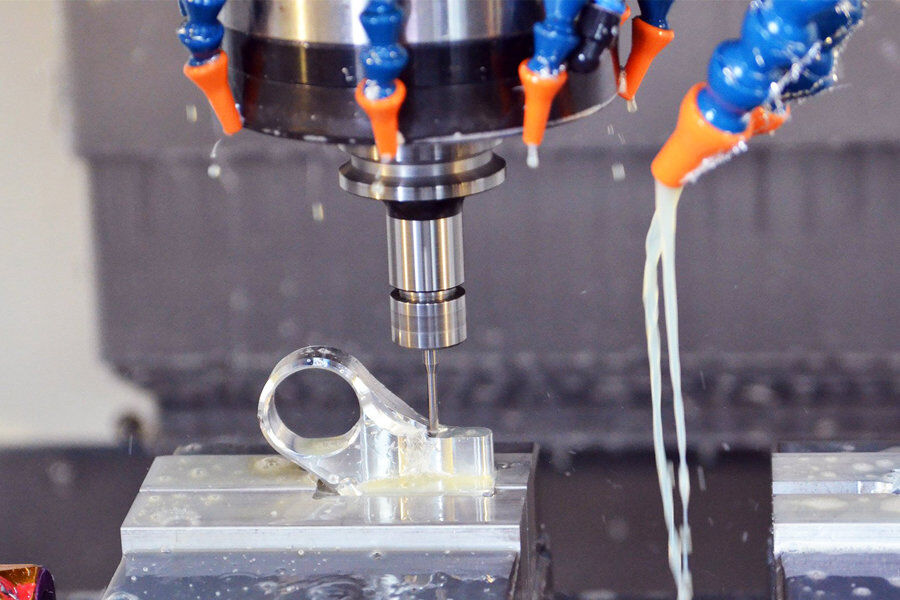
CNC Milling Services to Meet Quality Standards
We understand the challenges of production in an environment where components must meet certain standards in order to be acceptable. Everything we do is rigorously quality assessed at every stage. This enables us to not only produce exceptional components, but also to look critically at our processes in order to find further opportunities to cut costs and utilize turnkey solutions. Through a culture of continuous improvement, we are able to keep prices competitive without ever compromising on what you receive.
Ready to get started on your CNC milling quote?
What is CNC Milling?
CNC milling is a high-quality machining manufacturing process. Like CNC turning, it uses specialized CNC tools to machine raw materials, remove excess areas, and make custom parts. It belongs to subtractive forming manufacturing technology. It is also the most common processing technology for CNC services.
CNC Milling Process
Although CNC milling is a common secondary process to add finishing features to a part, it can also create finished, usable components out of raw materials for full production capabilities. The optimal type of milling equipment, design software, and cutting tools will vary depending upon a workpiece’s material and the part design. However, milling processes will typically involve:
1. CAD model design and conversion. First, the operator uses computer-aided design (CAD) software to generate a 2D or 3D model of the part. Once complete, computer-aided manufacturing (CAM) software receives the design and converts it into a program compatible with the CNC equipment, essentially translating the needed operations for the CNC machine to direct and control its actions.
2. Machine preparation. The operator prepares the milling equipment by securing the workpiece to the worktable, vise, or similar holding component. The required cutting tools are then selected and affixed to the spindle.
3. Process execution. After programming the design instructions and setting up the equipment, the machinist initiates the milling process. The cutting tool will progressively and selectively cut material away from the workpiece, rotating at speeds as high as thousands of RPMs for fast, efficient precision machining.
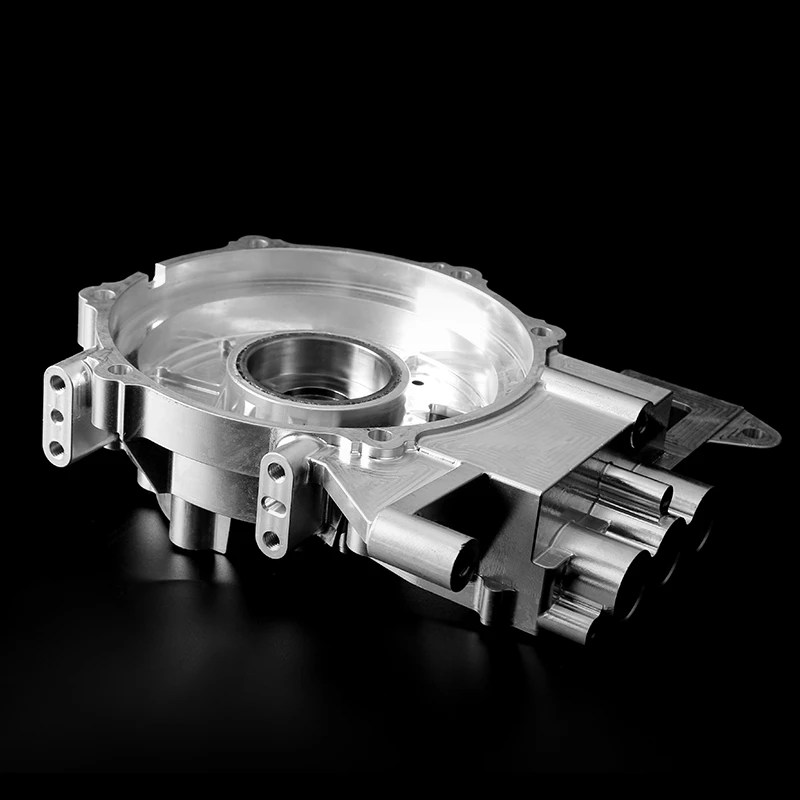
What kind of materials are worked on using the CNC milling service?
Due to the exceptional accuracy achieved by CNC machines, they are used primarily to form metal shapes. The most common is steel. It has a high degree of hardness, however that does not interfere with our machines capacity for precise machining. Stainless steel milling also includes related material groups such as austenitic or heat resistant. This range also includes structural steel, hardened steel, spring steel and many more.
A CNC milling machine can easily handle cast iron blocks (white, gray, black), aluminum and its alloys, tungsten, molybdenum or magnesium. It is also possible to mill copper, nickel super alloys or titanium, as well as various types of composites (especially thermoplastic and thermosetting plastics). But that’s not all. We can apply this specialized process to even a natural, relatively soft raw material like wood. So as you can see, a brand name CNC milling machine is a truly versatile device that can be used on almost any material.
Surface Finishes
1. Deburring: Tool marks and potentially sharp edges and burrs that exist on machined parts can be removed upon request.
2. Bead Spray: Gives a matte, smooth appearance to part surfaces.
3. Anodized (Type II or Type III): Parts can be anodized to different colors to create a corrosion-resistant surface.
4. Titanium anodizing is used in aerospace and medical device manufacturing. Can improve the fatigue strength and wear resistance of parts.
5. Passivation, Powder coating, Electrolytic polishing, Electroless Nickel, etc.
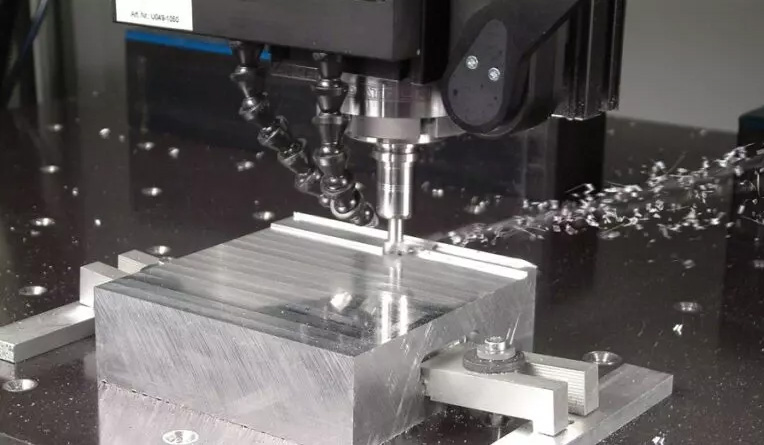
CNC Milling Applications
CNC milling is ideal for producing parts for a variety of industries, including:
1. Automotive. CNC milling is used to create parts for vehicles such as piston rods, pumps, flywheels, drive housings, engine blocks, and cylinders.
2. Aerospace. CNC milling is capable of producing parts with hard metals and other specialty materials necessary for the aerospace industry. Milling is crucial for the production of steering components and other aircraft parts.
3. Electronics. Precision CNC milling can create tiny, complex parts needed for motherboards and other electronic equipment.
4. Medical. CNC milling is used to create high tech medical equipment and tools, such as prosthetics, hip stems and cups, and cavity molds.
5. Military. CNC milling is capable of producing parts that meet the precision requirements for the military. It is used to create components for military technology, gun parts, and more.
6. Energy. CNC milling is used to create gears, valves, fuel pumps, and other elaborate components for air, hydroelectric, and nuclear energy applications.